Injection Molding
ThermoFab specializes in injection molding for heavy gauge plastic enclosures and related single use components for the medical device & life sciences and other critical highly regulated industries.
HEAVY GAUGE PLASTIC INJECTION MOLDING
At ThermoFab, our comprehensive suite of injection molding services is tailored to meet your enclosure development needs. Our skilled team provides guidance on prototype development, process engineering efficiencies, surface finishing, and assembly. With extensive experience in large multi-part projects from heavy gauge plastic enclosures for medical devices to singe use components for autonomous robots, and housings for genetic sequencing devices, we provide solutions to meet your needs.
Injection molding’s custom design capabilities has driven the popularity of the high mix, low volume (HMLV) production strategy. The flexibility of HMLV enables seamless design changes and customizations, giving you a competitive edge in your market. Integral to our comprehensive services is our unwavering commitment to quality management practices, which is emphasized by our ISO 9001 certification. This ensures that every product meets your project requirements.
Check out our case studies for more information
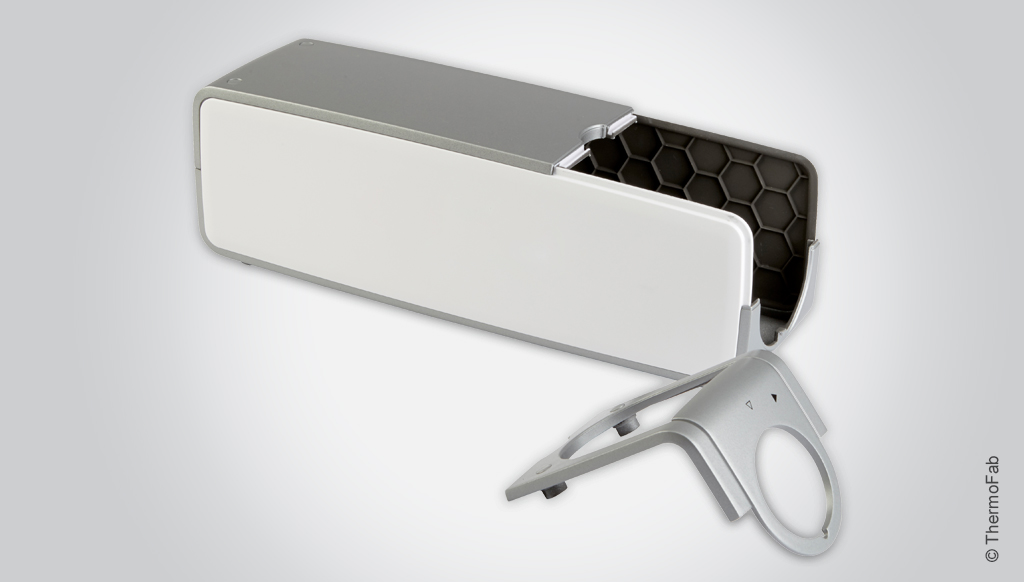
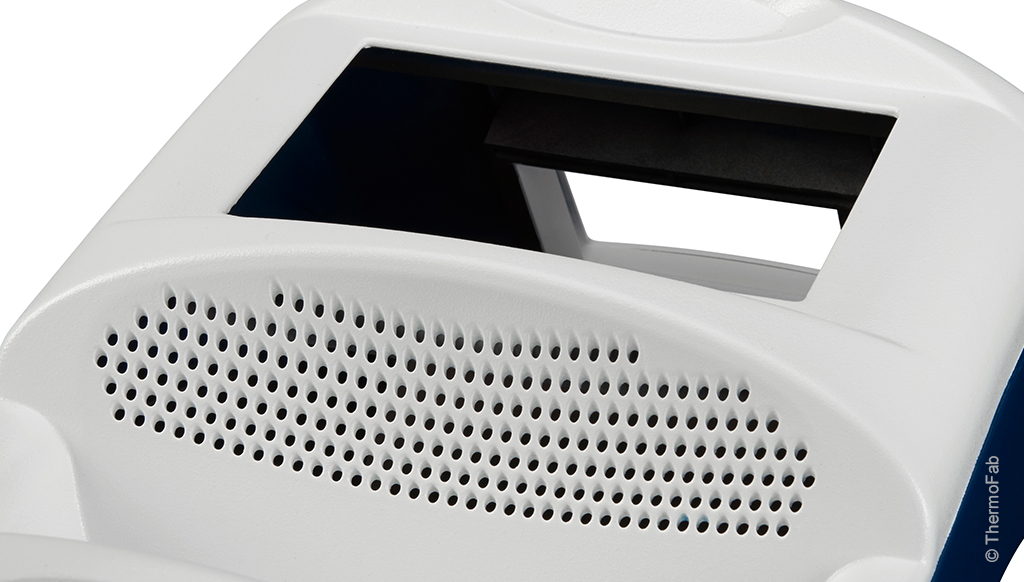
ADVANTAGES OF INJECTION MOLDING
Injection molding provides multiples benefits, making it a preferred choice for manufacturers looking to produce a wide range of products for larger production runs.
- High Efficiency & Speed: this process allows for the production of large quantities of parts (500-10,000) at a rapid pace
- Cost-Effectiveness: despite initial setup costs, injection molding is highly cost-effective for large production runs, with each part only taking seconds to a few minutes to mold
- Complex Geometry: parts can be produced with intricate and complex shapes that are difficult to achieve with other manufacturing processes
- Flexibility: injection molding allows for the use of exotic materials like translucents, transparents or elastomerics, resulting in a distinctive and functional product design
- Consistency & Repeatability: this process ensures each part produced is virtually identical to the next one
- Customization: parts can be easily customized to incorporate branding elements using painting, silk screening or pad printing
size capabilities
With our cutting-edge manufacturing capabilities, we’re equipped to produce components of various sizes. Whether you require intricate designs or larger-scale productions, we can accommodate your needs with precision and efficiency. Additionally, our expertise extends to achieving a wide range of part wall thicknesses, ensuring optimal performance for your applications.
- Can manufacture components up to to 1.8m (70″) x 1.2m (47″) x 1m (40″)
- Part wall thickness from .04” to .38” (1 mm to 10 mm)
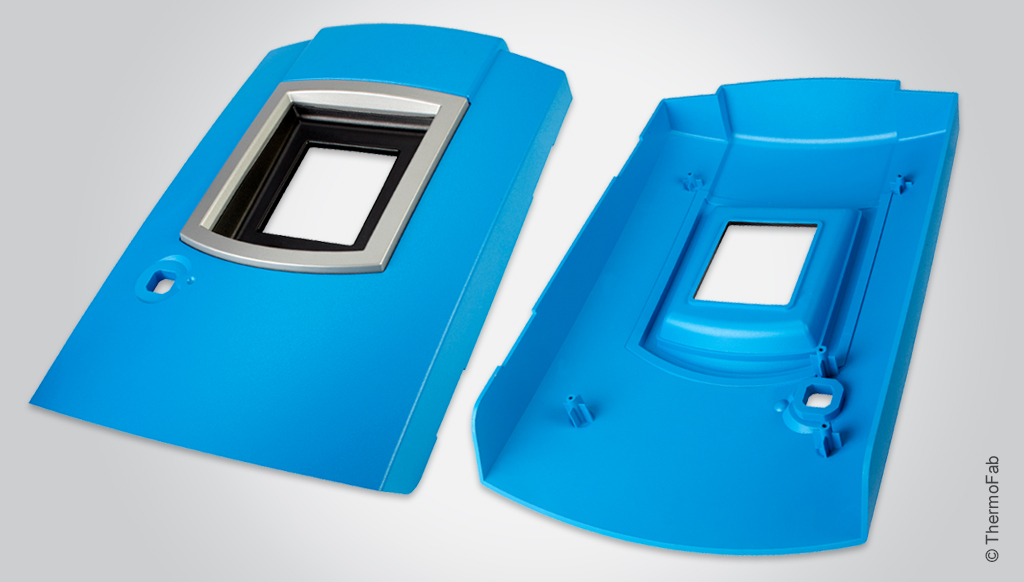
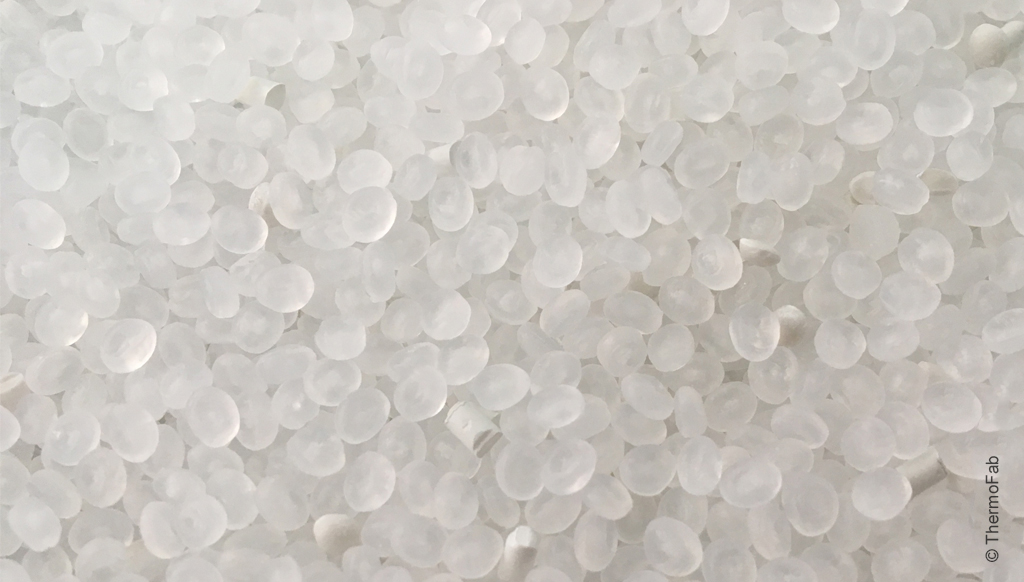
materials of construction
If you need assistance, we can help with material selection from our comprehensive list of typical engineering plastics below. If you would like to request custom or additional materials, we are happy to discuss those options with you.
- Starex Flame-retardant ABS
- Kydex Acrylic/PVC
- Sabic Polycarbonate ABS blends
- Polycarbonate
- ABS
- PVC
- Acrylics
- High impact polystyrene (HIPS)
- Polypropylene
- HDPE
- Exotic materials: translucents, transparents & elastomerics